Smart Mobility
SMART MOBILITY
Open mobility platform
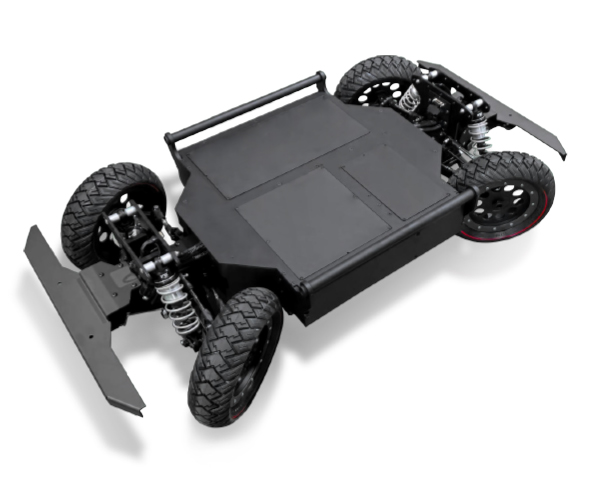
TM-1
Multi-purpose 4-wheel steering, 4-wheel drive
mobility platform capable of off-road driving
TM-1 is a multi-purpose educational and research mobility platform independently developed by TREEZE Engineering based on the technology and experience accumulated through years of autonomous driving mobility development.
TM-1 is equipped with a 4-wheel steering 4-wheel drive system and is equipped with an electric drive-type chassis module that can achieve stable driving performance even off-road by applying a low center of gravity design to minimize the risk of rollover.
It has an optimal base shape for implementing various forms of mobility and was developed to easily supply power to the upper system and implement communication.
Spec
Maximum load 25 kg
Aluminum body applied
Max Steer Angle < 30°
(Option: 4-wheel independent steering)
(Option / Soft Type: Diameter 265mm * Width 85mm)
(equipped with height adjustment function : 2 levels)
STM32
CAN 2.0B support
Key Features
(option)
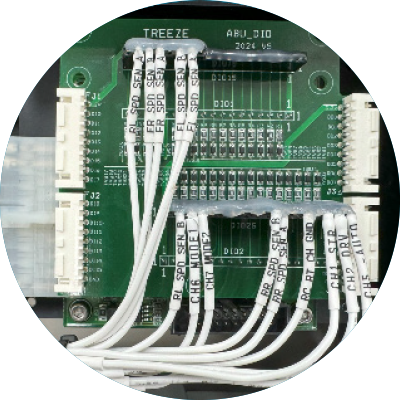
dedicated VCU
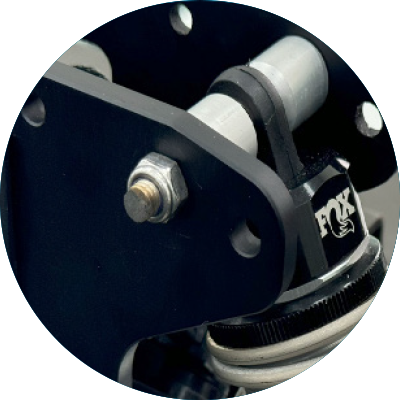
is functional
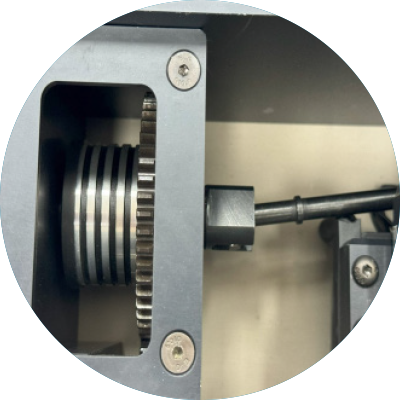
differential application
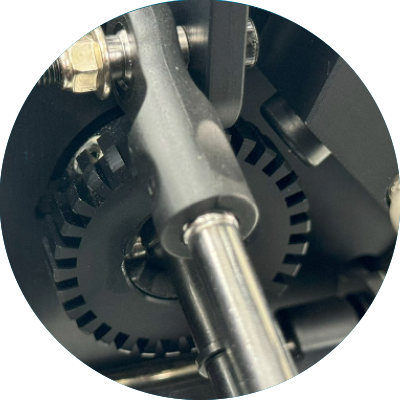
dedicated VCU
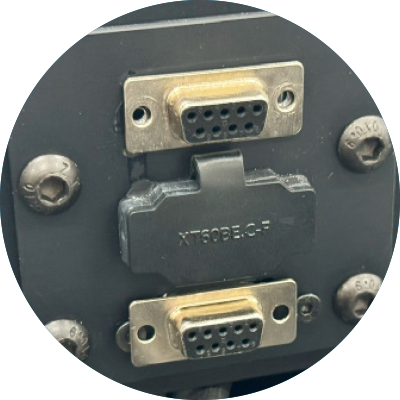
is functional
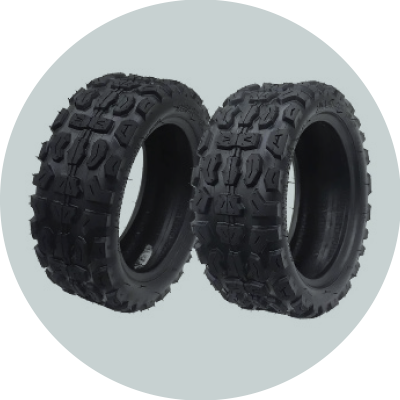
differential application
Key Point
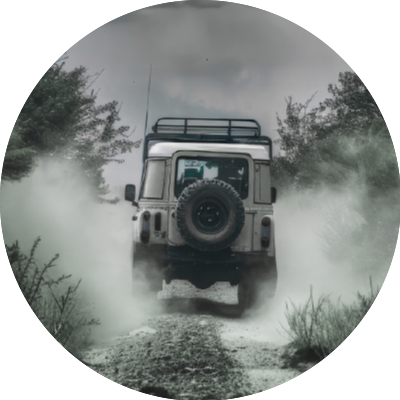
driving
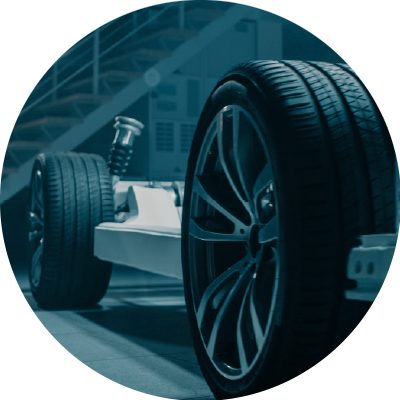
4-wheel drive
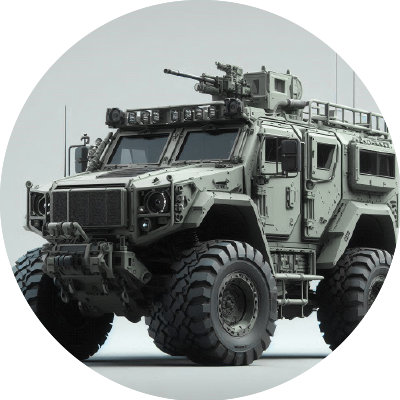
various purposes
* In addition to the basic supplied specifications, TM-1 supports custom manufacturing according to various customer needs.
Customer-tailored
production support
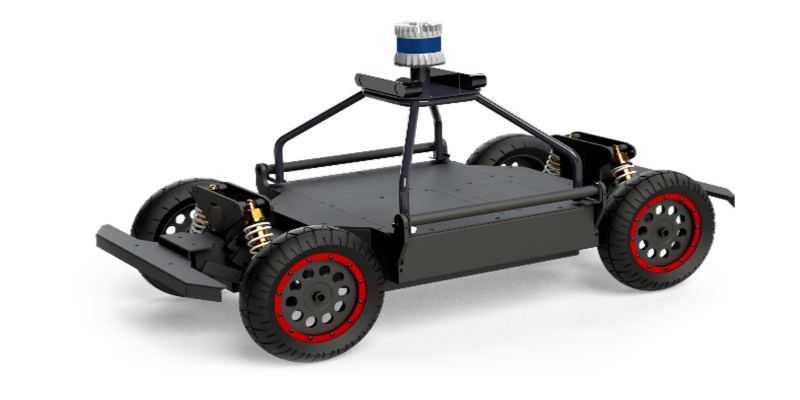

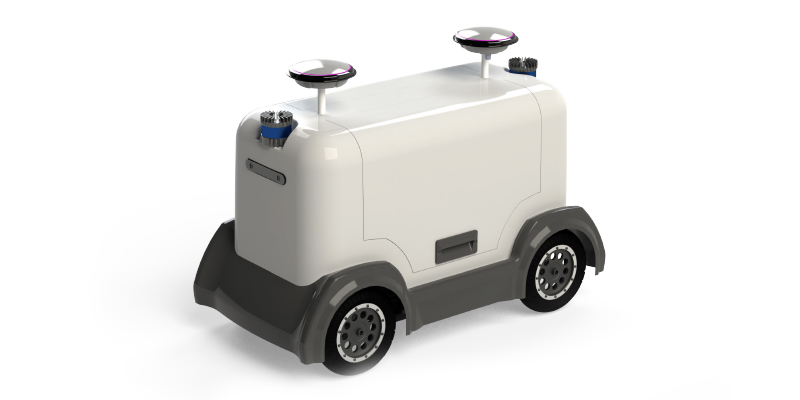
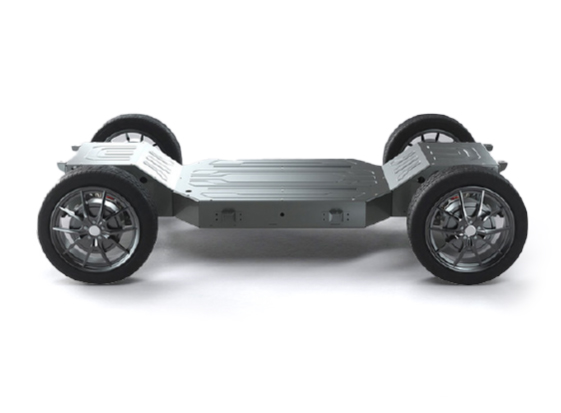
OPERA LOOP
Full-Drive-by-Wire Skateboard Chassis Platform, an EV mobility platform optimized for the development of actual car-sized autonomous driving
- In-wheel motor / various steering modes
(2WD, 4WD, independently controlled 4WD) - Multi-purpose autonomous driving platform that can be customized/expanded
- Open CAN interface / open source SW (Autoware) support
- Includes safety device features
Spec
Product basic configuration
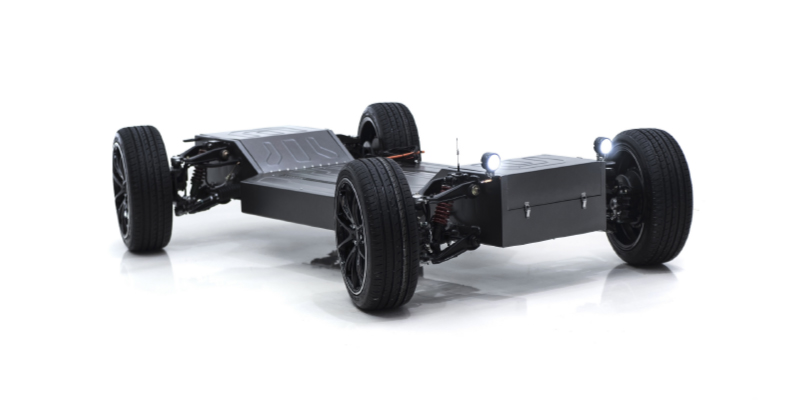
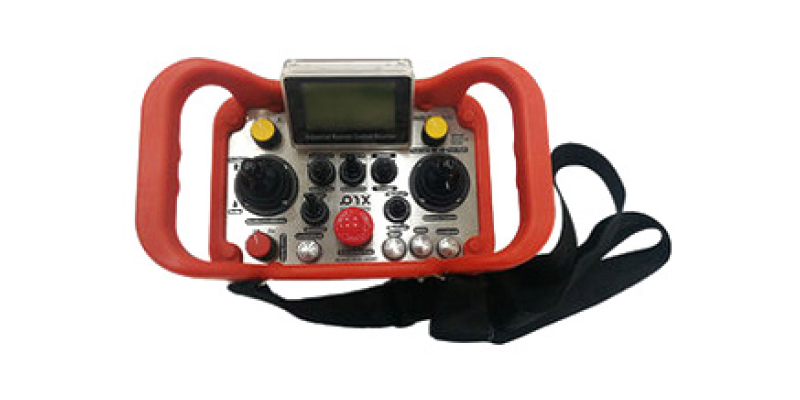
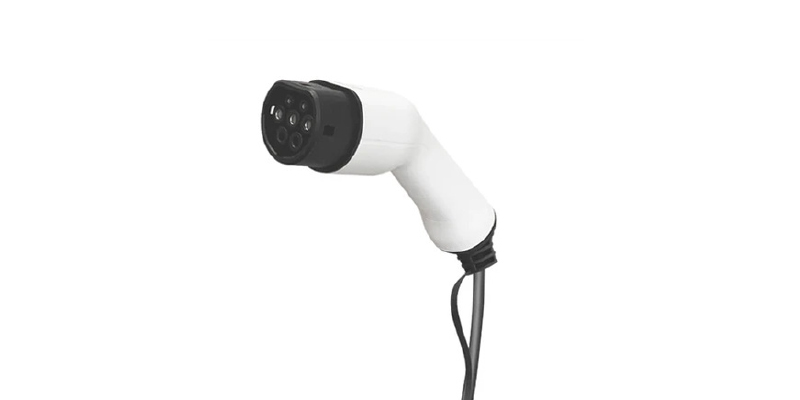
Option
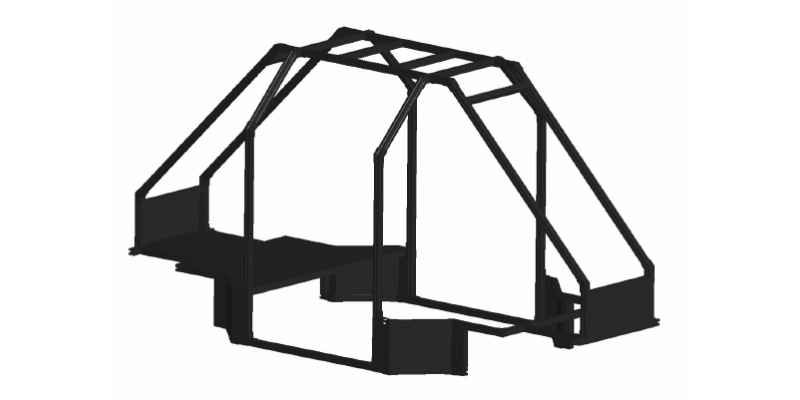
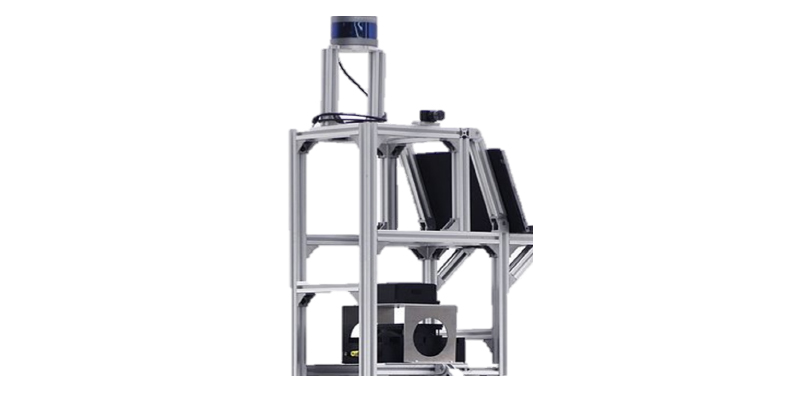
Lidar/Radar/Camera, etc.
(Customized production supported)
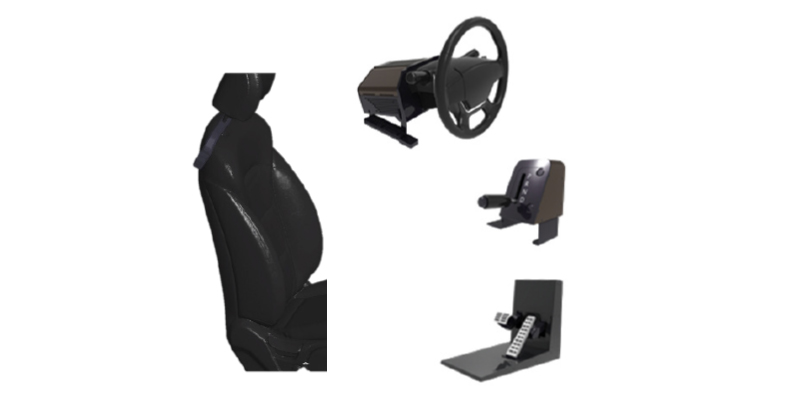
- Steering wheel
- Accelerator, Brake pedal
- IO box for operation
- Driving seat
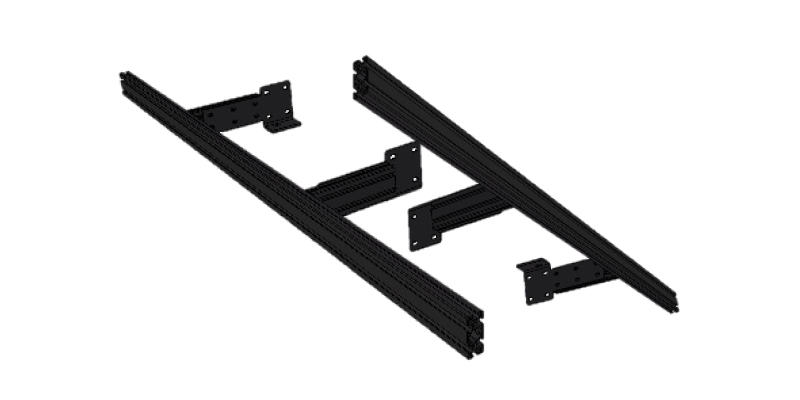
- Front and rear bumpers (1 set)
- Built-in collision detection sensor
Pakage
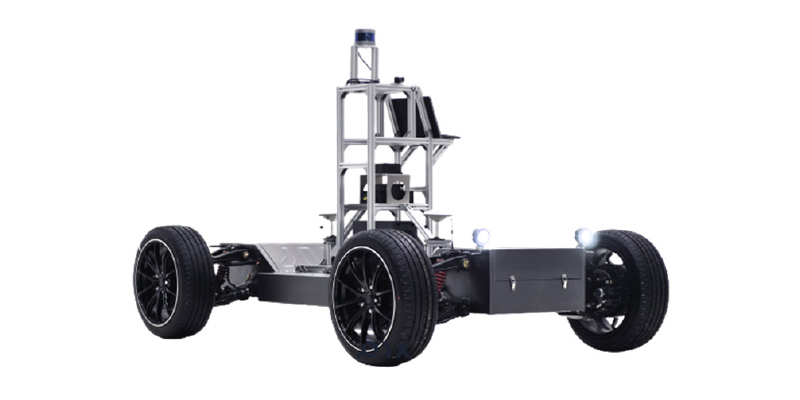
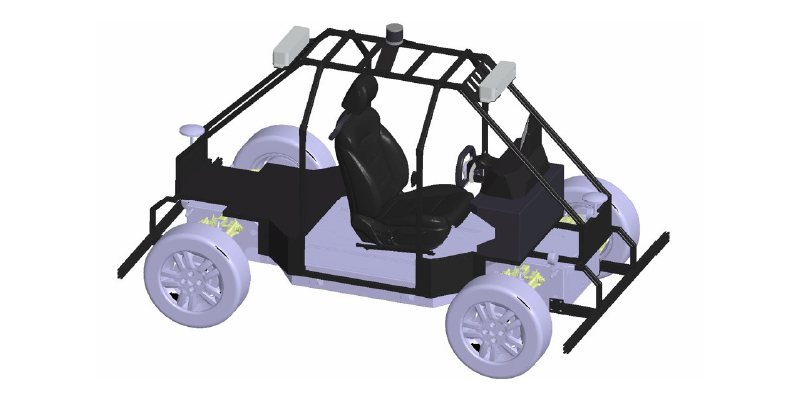
Support for custom / expanded mobility production
We provide the best autonomous driving solutions with customized manufacturing and
various options optimized for customer needs and purposes.
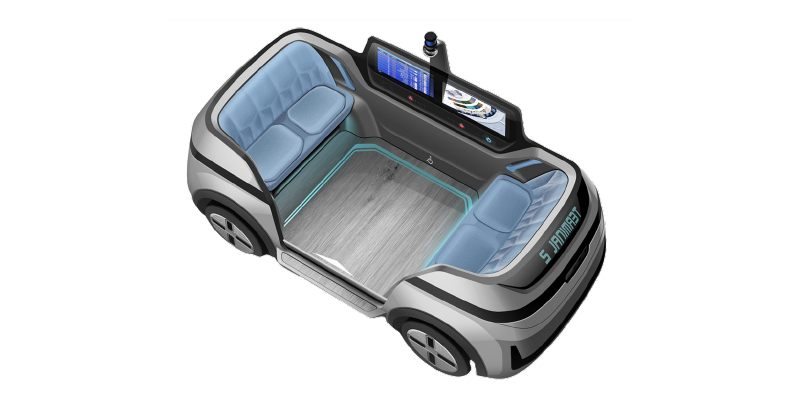
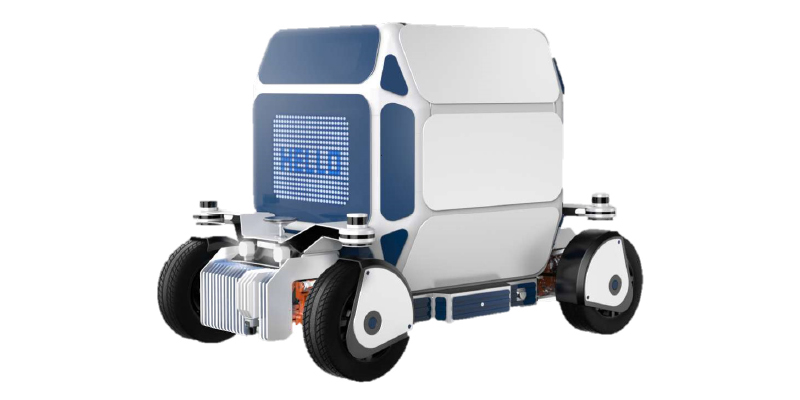
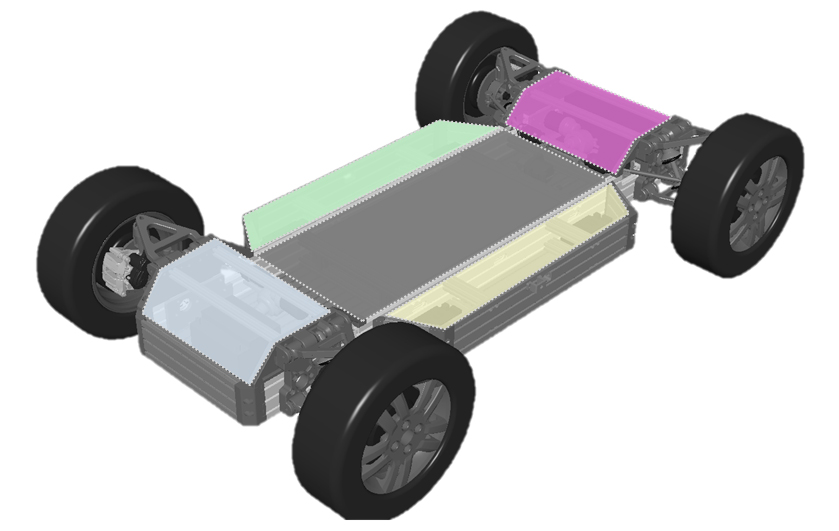
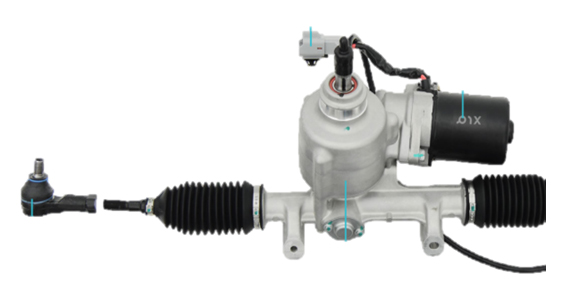
Steering Controller
- – 4 Wheel Steering Control
- – 12V DC power supply
- – 1 DC motor drive
- – CAN interface
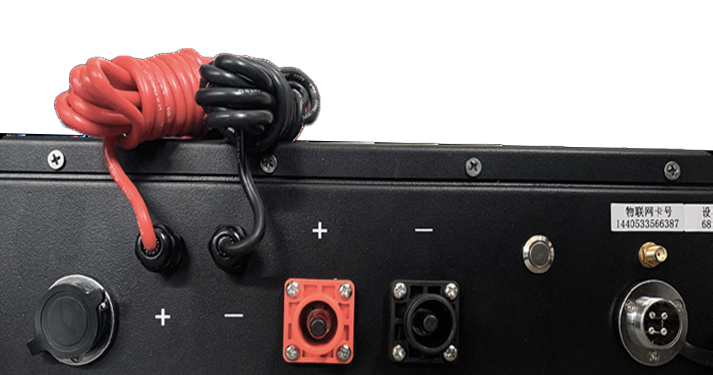
Battery Management System
- – Voltage/power/temperature output
- – Charging interface
- – Has battery protection logic (overcharge / overcurrent / voltage imbalance)
- – CAN interface
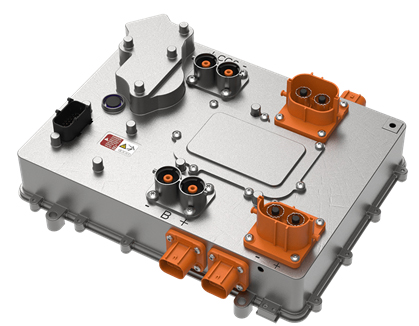
– DC Power System
- – Hub motor power distribution
- – Chassis / body / autonomous driving module power supply
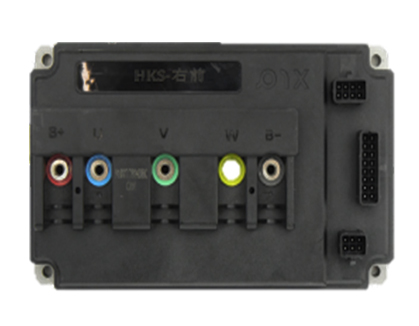
Hub Motor Drive
- – Hub motor driving circuit module
- – Input voltage 72V DC / 3 phase
- – Hub motor connection
- – CAN interface provided
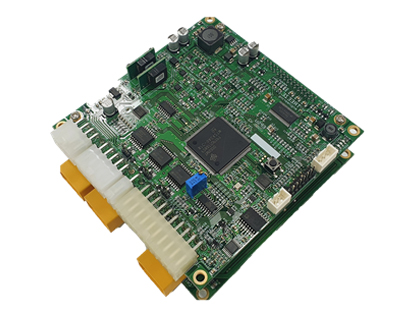
Vehicle Control Unit
- – Drive control
- – Braking control
- – Steering control
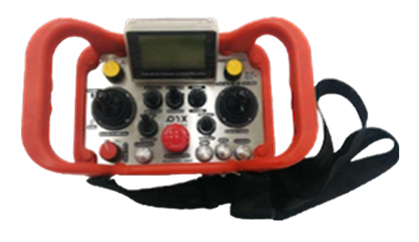
Remote controller for manual control
- – Controller for operating the vehicle when the operator is on board
- – Vehicle can be operated from outside using the X-by Wire system
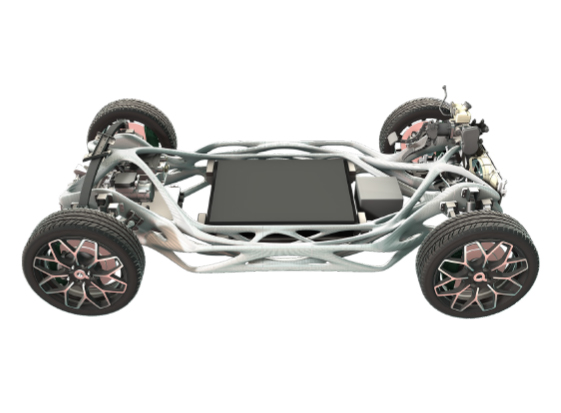
ROBO-EV
EV Chassis Platform with ultra-small mobility standards
- Ultra-compact (1-2seater) standard EV platform
- Light body and excellent mileage
- Excellent ride comfort thanks to double-wishbone suspension
- Front wheel steering, rear wheel drive type
- All-in-one (3D printed) frame applied
- Simultaneously equipped with manual operation + Drive By Wire function
Spec
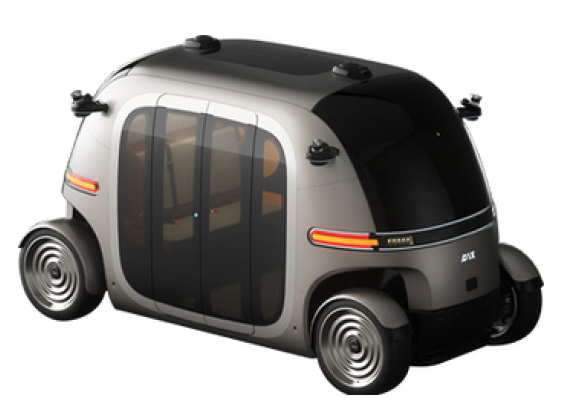
ROBOBUS
Self-driving shuttle-type mobility using an open mobility platform and Level 4 autonomous driving technology
- Vehicle design optimized for shuttle/taxi services
- Equipped with autonomous driving level 4 technology
- Implementation within 2-3 days from mapping to actual service
- Equipped with safe driving technology through various empirical cases
- Comfortable interior space (capacity : 6 people)
- Four-wheel drive, four-wheel steering system applied
- Ensuring convenience of maintenance by applying modular design
- Apply multiple safety systems
Spec
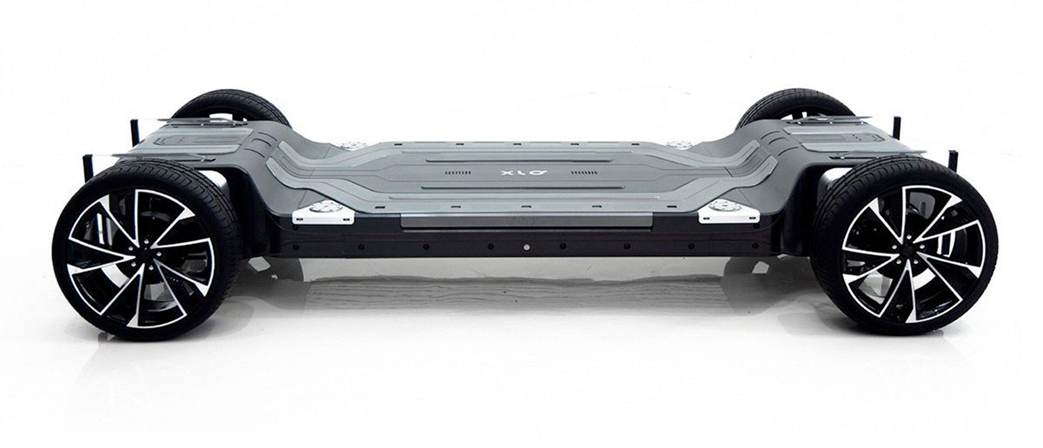
* Robobus is equipped with a variety of sensor packages (LiDAR, cameras, navigation systems, etc.)
and a multi-layer safety redundancy system to provide safe and efficient autonomous driving.
Autonomous driving
The self-driving software installed in Robobus is Autoware Universe, a globally recognized open source-based self-driving car SW platform.
Using Autoware, we implemented safe autonomous driving by recognizing driving conditions (obstacles, lane markings, traffic lights, etc.) through various sensors such as cameras, lidar, and INS installed on the robobus.
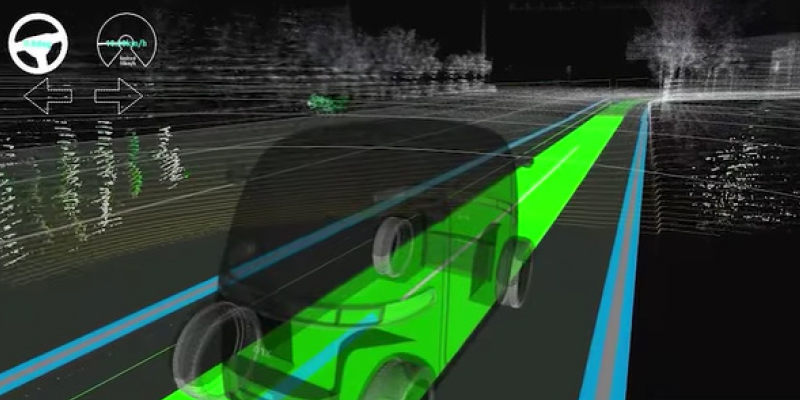

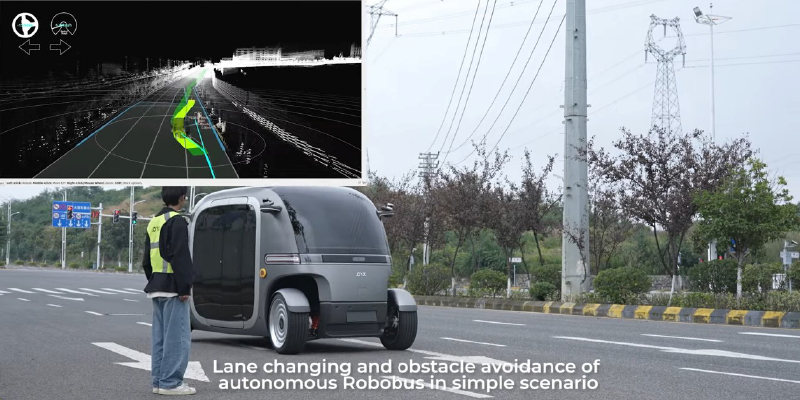
Use cases
Suitable for offices, mobile shops, and brand promotion spaces
Robobus, which has a beautiful exterior, can be used for a variety of purposes by utilizing efficient technologies such as autonomous driving and remote driving. It can be used as an office, and you can get closer to customers with mobile shops such as select shops, food trucks, and brand promotion centers that can sell or promote products.
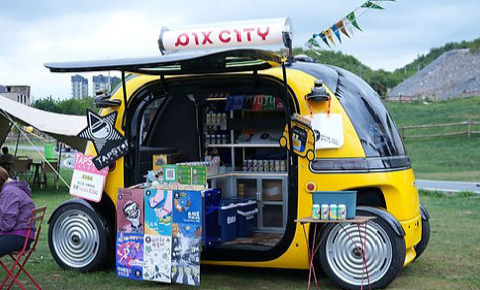
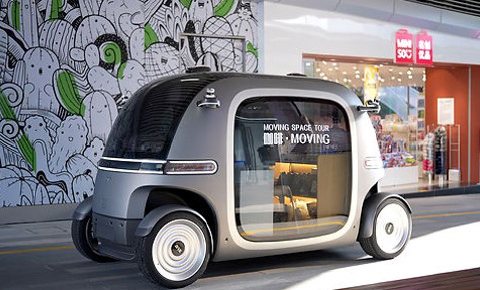
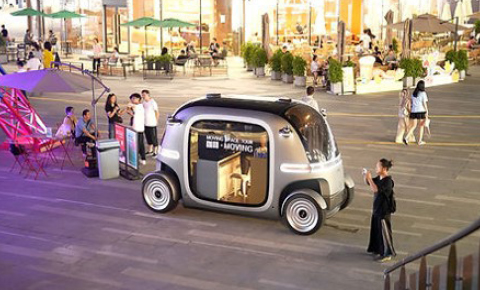
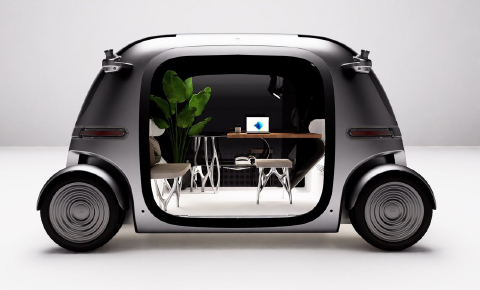
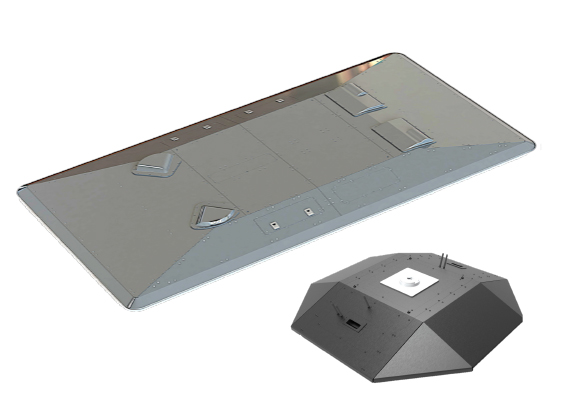
OFR (Overrunable Flat Robot)
For verification of autonomous driving / ADAS performance and safety
Self-driving dummy robot platform
OFR is an AGV (Automated Guide Vehicle) robot platform that can move according to a set scenario by installing a Target Vehicle or Target Pedestrian model on top.
OFR has a function that allows the target car to safely pass over the target when the ego and target collide. This function enables repeated quantitative testing of target vehicles. It is equipped with a driving/suspension/braking device specially designed for this function, and the target car has a maximum speed of 80kph.
Spec
OFR_Vehicle | OFR-Pedestrian/Bike | |
---|---|---|
Dimensions | 3,170 x 1,690 x 100 | 1,000 x 1,000 x 100 (85) |
Clearance | < 40 mm (Adjustable) | > 40 mm |
Weight | 275 kg | 80 kg |
Payload | 120 kg (DRITM Soft Car 360) | 30 kg (Soft Pedestrian Target) |
Speed | 80 km/h | 10(40) km/h |
Acceleration | 3 m/s2 | 1(3) m/s2 |
Braking | -8 m/s2 (Hydraulics) | -8 m/s2 |
Control Modes | Waypoint & Manual(W/ Joystick) | ← |
Network | LTE, WIFI, RF-Radio(Remote Controller) | ← |
ETC | Replaceable battery, air suspension, control room integrated control | ← |
Managing SW
for Multi-OFR
-
Scenario design/editing
-
Multi-object synchronization support
-
Built-in robot status data monitoring / saving / analysis function
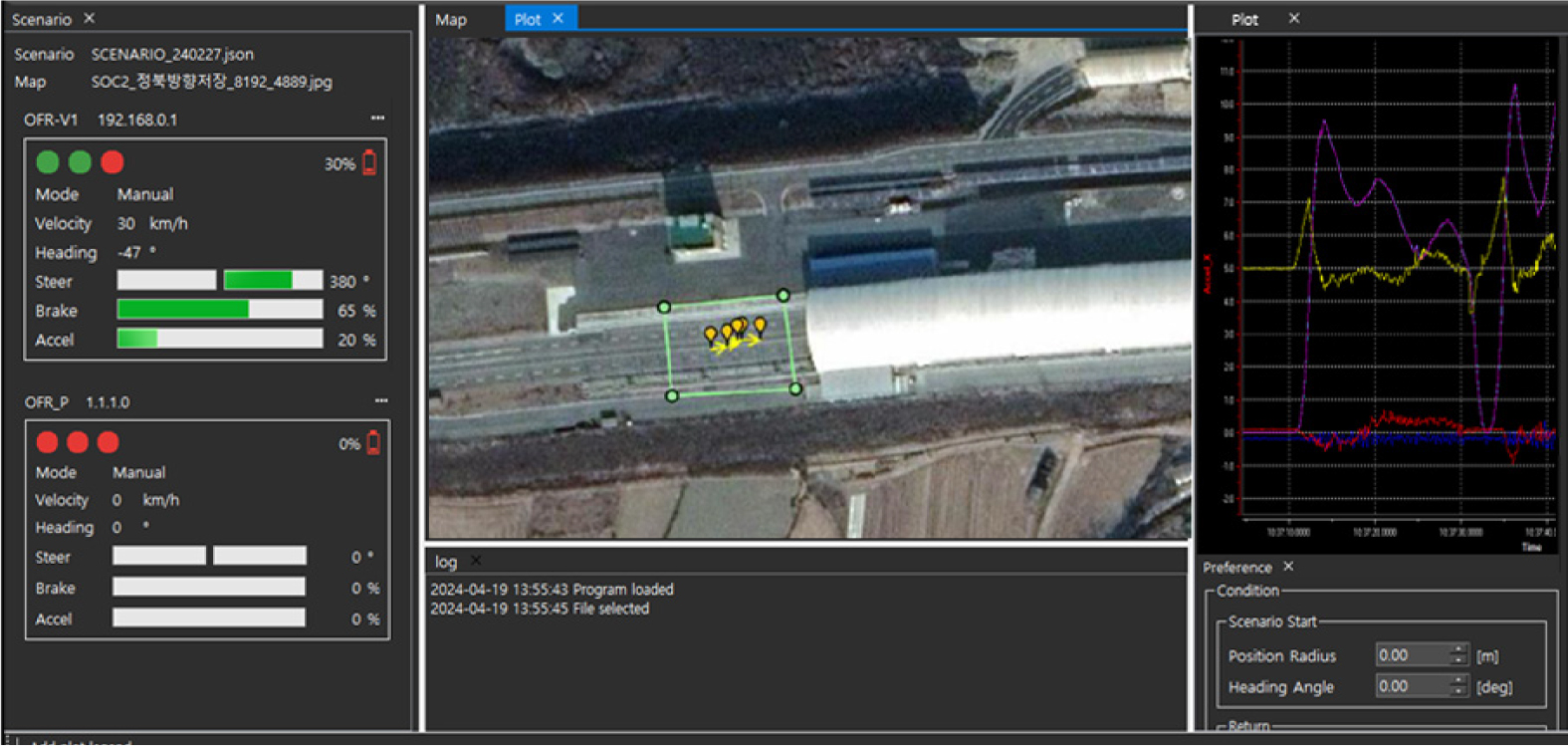
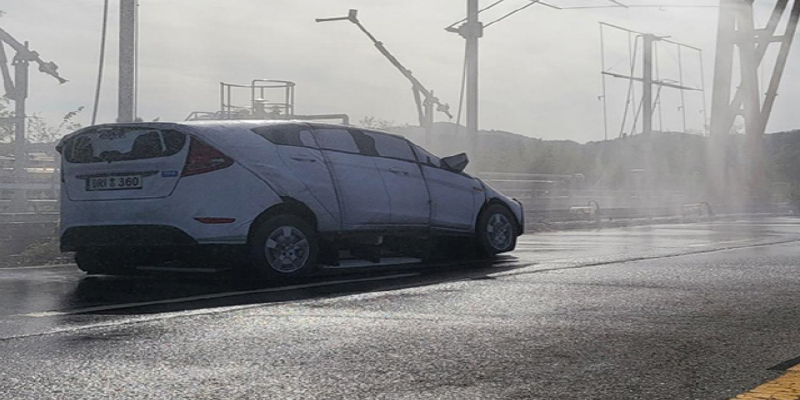
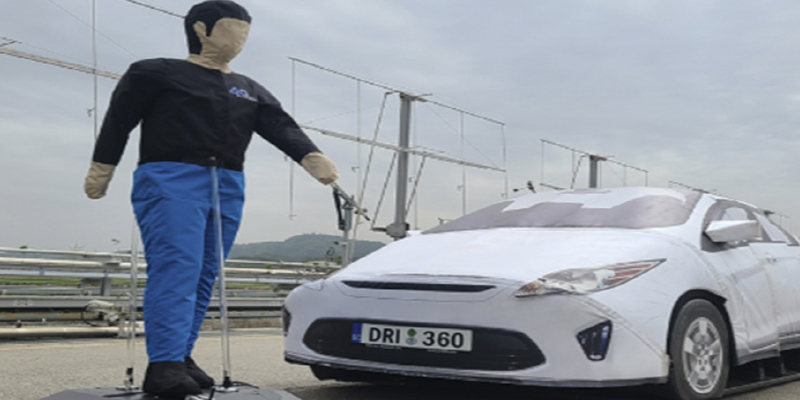
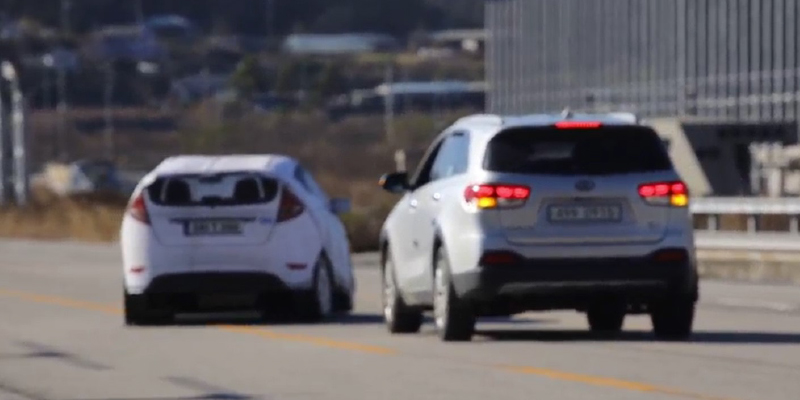
OFR-V detailed specifications | ||||
---|---|---|---|---|
Maximum speed | 60km/h | |||
Maximum acceleration | 0.3g | |||
Maximum deceleration | 0.8g (dry road surface) | |||
Maximum lateral acceleration | 0.3~0.4g | |||
Weight | 275kg | |||
Length | 3170mm | |||
Width | 1690mm | |||
Height | 100mm | |||
Wheel base | 1620mm | |||
Front overhang | 865mm | |||
After overhang | 685mm | |||
Ground clearance | 30mm |
Driving battery detailed specifications | System battery detailed specifications | ||
---|---|---|---|
Capacity per battery pack / Total capacity | 710.4Wh / 2.84kWh | Battery capacity | 1.55kWh |
Number of battery packs | 4 | Number of batteries | 1 |
Cells per battery pack | 12S | Cells per battery pack | 7S |
Cell nominal voltage | 3.7V | Cell nominal voltage | 3.7 |
Cell maximum charging voltage | 4.2V | Cell maximum charging voltage | 4.2 |
Cell nominal capacity | 16Ah | Cell nominal capacity | 60Ah |
Maximum continuous discharge rate | 25C | Maximum continuous discharge rate | – |
Maximum continuous discharge current | 400A | Maximum continuous discharge current | 100A |
Maximum continuous charge rate | 3~5C | Maximum continuous charge rate | – |
Maximum continuous charge current (recommended) | 80A(15A) | Maximum continuous charge current (recommended) | 10A |
Cutoff discharge voltage | 3.3V | Cutoff discharge voltage | 3.3V |